Optical Film Coating Equipment Series
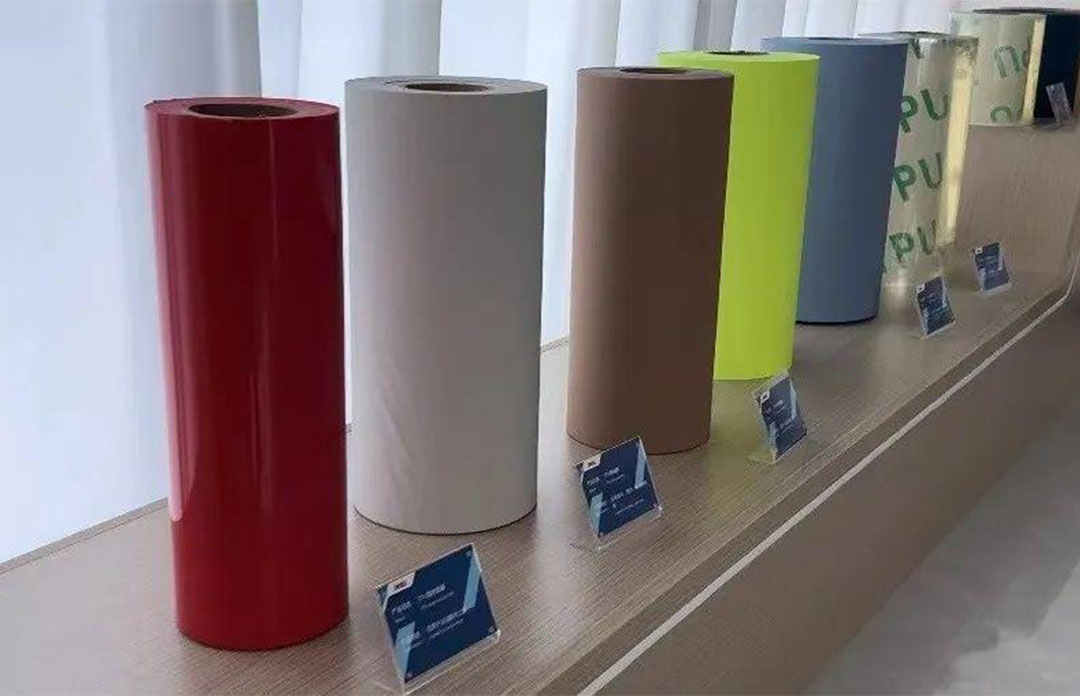
With the extensive use of plastic film materials, plastic materials have shown a revolutionary development. With the continuous progress of the plastic extrusion industry, JWELL has overcome the barriers of related technologies and production processes, and today we would like to introduce to you a series of multi-functional plastic film coating equipments from JWELL - Optical products.
Equipment introduction
Optical film coating equipment consists of unwinding unit, unwinding storage unit (protective film peeling and winding), front traction unit (with preheating and shaping group), coating unit (precision slit extrusion coating unit + micro-concave kiss coating coating unit), vacuum adsorption traction unit at the oven inlet, oven heating (energy saving and emission reduction) unit + light curing unit, cooling and deskewing unit at the outlet of the oven, the second unwinding unit, protective film composite cooling and shaping traction unit, winding storage unit and winding unit. unit, winding storage unit, winding unit. Through the free matching of each component, it can be applied to optical products such as car coat film, optical film, explosion-proof heat insulation film, tactile film, hardened film, flexible circuit board and release film. Coating base film materials: TPU, PI, PE, PET, aluminum foil, copper foil, paper, etc.
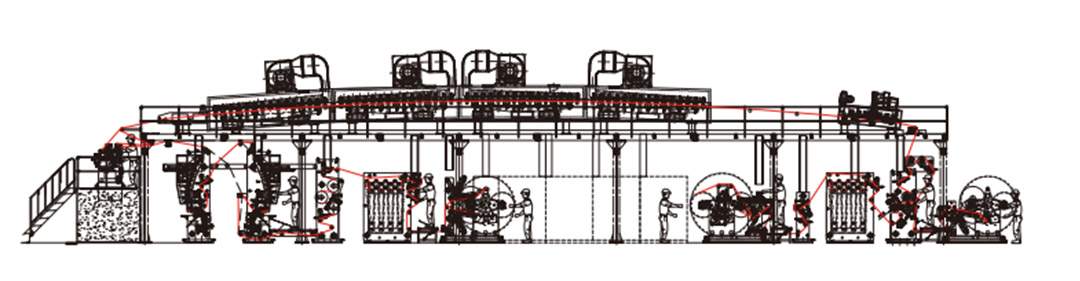
Advantages of the equipment
The optical film coating equipment adopts advanced design concepts, with ultra-high precision overall control performance, high-precision coating quality metering control, high sensitivity tension detection mechanism and other advanced control and detection systems, to realize the production line's automation and stable production as well as intelligent control mode.
Product Application
TPU Car Film
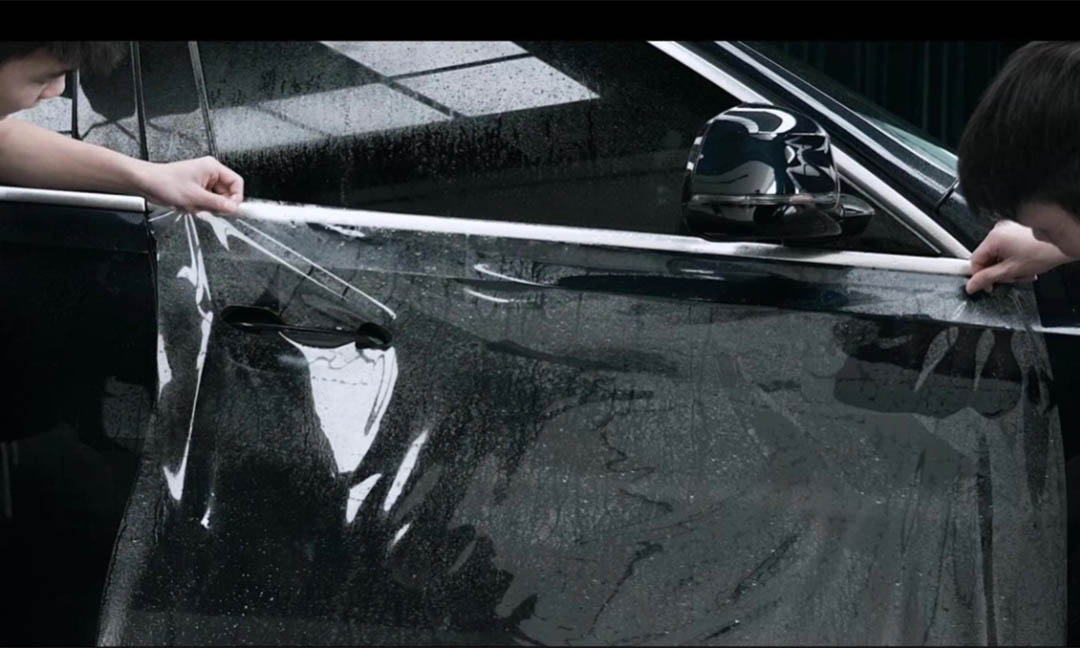
Car coat film, also known as paint protection film, conventional process production flow: TPU base film + double-sided coating (functional self-repairing layer + adhesive backing) + protection film composition. PET film has been preferred as a car coat because of its high strength, high heat resistance, chemical corrosion resistance and other advantages.
Invisible car coat coating mainly adopts slit coating process, which is divided into two kinds of coating glue and coating functional layer.
Optical Film
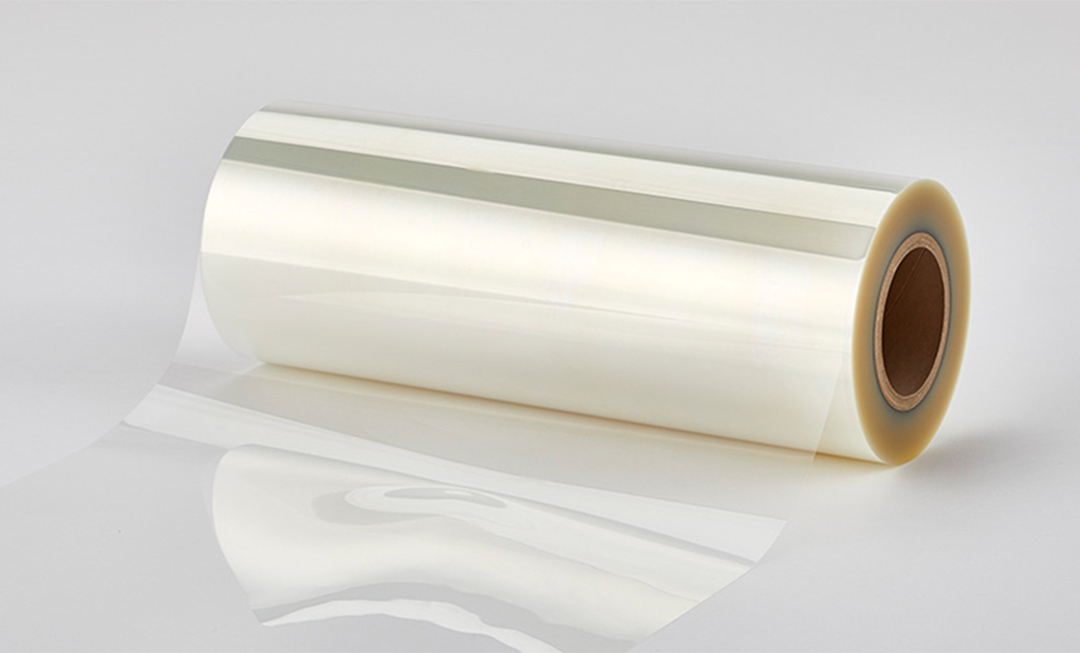
LCD adopts PET as the base film, and adds various coating agents on the surface of PET to give it all kinds of optical properties and realize its various products for various purposes: the types of coating agents are: high refractive index, color photoresist/black photoresist, photochromic, optical adhesive, and so on, a series of coating agents. The realized applications are: color filters, reflective films, anti-reflective films, prism sheets, liquid crystal orientation films, interlayer insulation coatings, and transparent conductive films. As for the coating unit, a precision slit extrusion coating unit and a micro-gravure reverse kiss coating unit are generally used.
Silicone Protrctive Film
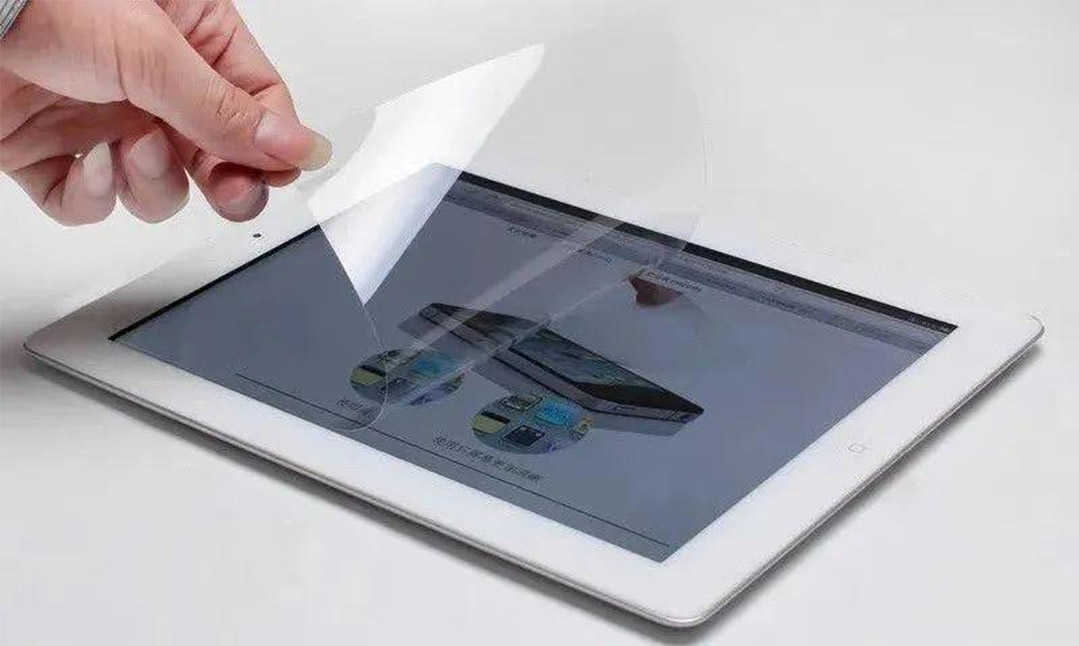
Silicone protective film is one of the common protective films on the market, coated with silicone from optical grade transparent PET base film, can be laminated with release film processing into a double-layer silicone protective film. General use of high-precision extrusion coating process to prepare and become, the preparation process should ensure that its cleanliness and light transmittance and other indicators, and no white spots, white fog, sand holes, wire drawing, scratches and other phenomena.
Hard Coated Film
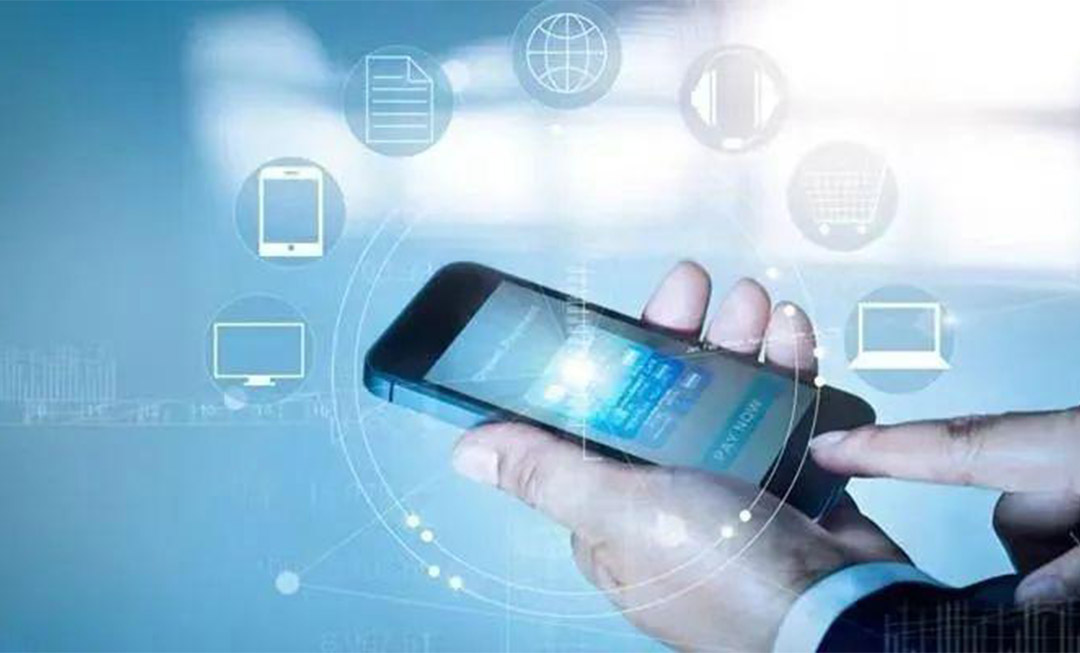
The hard coated film is usually made up of a layer of transparent cellulose acetate or polyimide film, coated on the surface of the base material, through a special baking process, the film and glass firmly through the drying and curing process, the surface of the substrate to form a layer of hardened layer. The advantages of the hardened film are thin and transparent, and it can improve the functions of the substrate such as UV resistance, abrasion resistance, anti-charging, fingerprint resistance, and anti-fouling.
The appearance of hardened film coating is mainly manifested in terms of flatness, gloss, distortion, color and so on. Flatness refers to whether the surface of the hardened film is flat, whether there are bumps, cracks and other defects. Glossiness refers to the reflective ability of the surface of the hardened film, generally speaking the smoother, the better the reflection.
Production Line Specification
Equipment specification | 1250-2000 mm |
Operating speed | Max.150 m/min |
Base material width | 300-2000 mm |
Coating method | Precision Slit Extrusion Coating Unit, Micro-Gravure Reverse Kiss Coating Unit, Comma Blade Coating Unit |
Unwind/Winding Diameter | Φ800 mm |
Splicing method | Automatic connection without stopping the machine |
"Excellent Quality, Perfect All" is Jwell's quality policy, and all staff's working direction.