Daily operation preparation
Safety check points before starting
Before starting the machine, it is necessary to carefully check whether all the safety protection devices of the extruder are intact and ensure that the protective door, emergency stop button and safety light curtain are in normal working condition to prevent accidental injuries during operation.
Before the operation of the extruder equipment at high temperature, it is important to check the oil level and grease quality of the lubrication system to ensure that the moving parts are fully lubricated to avoid equipment wear or failure due to insufficient lubrication.
Before starting the machine, the electrical system should be thoroughly checked to ensure that all wiring is firm, no exposure, no debris in the electric control box, prevent electrical short circuit or fire, and ensure the stable and safe operation of the extruder equipment in a high temperature environment.
Setting and adjusting the heating temperature of the tank
When setting the heating temperature of the tank, it is necessary to consider the melting point and fluidity of the material to ensure that the material can be uniformly heated during the extrusion process to avoid incomplete melting of the material caused by too low temperature or material degradation caused by too high temperature.
When adjusting the heating temperature of the tank, a base temperature should be preset according to the material type, and then fine-tuned by the actual extrusion effect until the optimal melting state is reached, this process may require several tests to determine the optimal temperature.
In order to ensure the stability and accuracy of the heating temperature of the tank, it is necessary to regularly use professional equipment to test and calibrate the heating system, while monitoring the working condition of the heating elements, timely replacement of damaged parts, and ensure accurate temperature control during the extrusion process.
Control and influence of plastic filling amount
The amount of plastic filling directly affects the density and dimensional stability of the product, and excessive or insufficient will cause defects in the product. Precise control of the filling amount is a key step to ensure product quality.
Through experiments and data analysis, the optimal filling range can be determined to improve production efficiency and reduce material waste. Adjust equipment parameters regularly to meet the needs of different production batches.
Establish a real-time monitoring system to adjust the filling amount in time to ensure the stability of the production process. Automation technology is used to improve the control precision of filling quantity and reduce human error.
Cleaning and maintenance
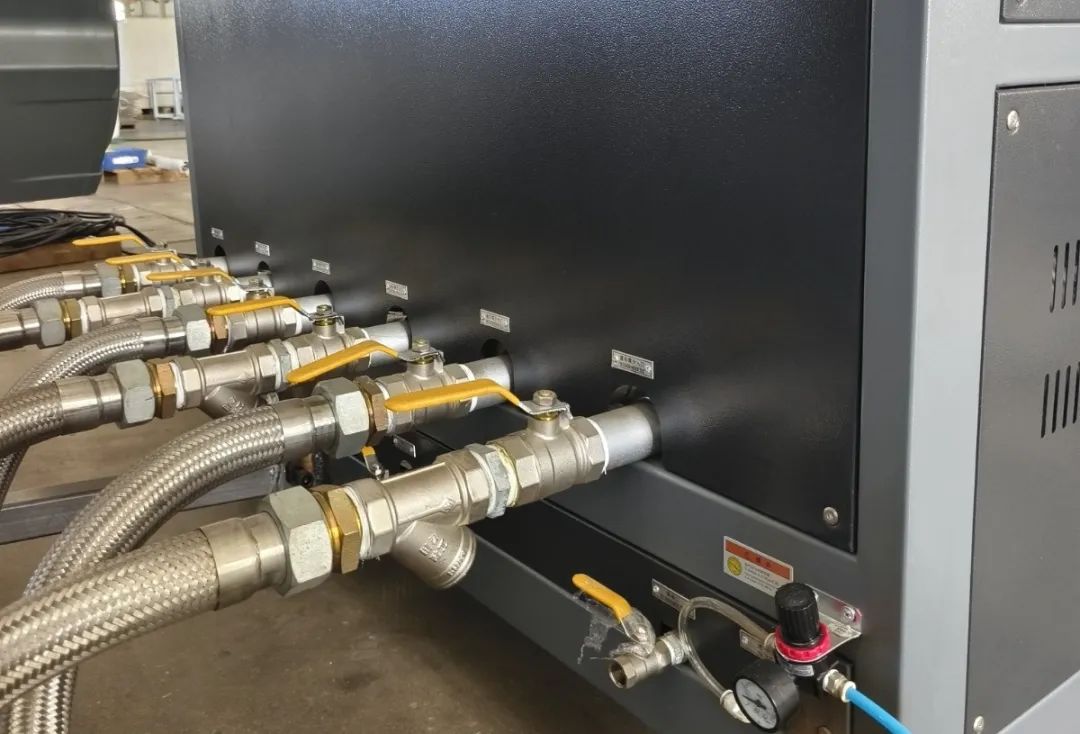
Regular cleaning of the cooling system can effectively remove dirt and sediment inside the system, which will reduce the heat exchange efficiency, resulting in reduced cooling effect. Through cleaning, it can ensure the efficient operation of the system and maintain the best working condition of the equipment.
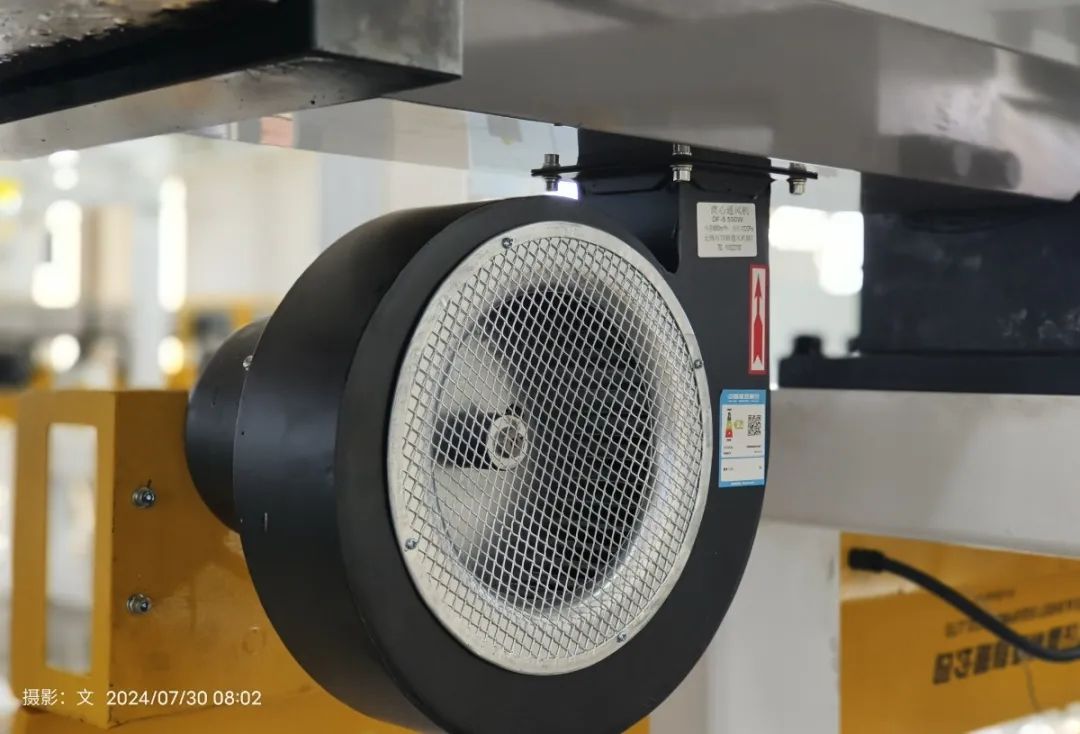
Dirt and deposits that accumulate in the cooling system not only affect performance, but can also corrode components and shorten equipment life. Regular cleaning and maintenance can help prevent this damage, thereby extending the life of equipment such as extruders and reducing the frequency of replacement.
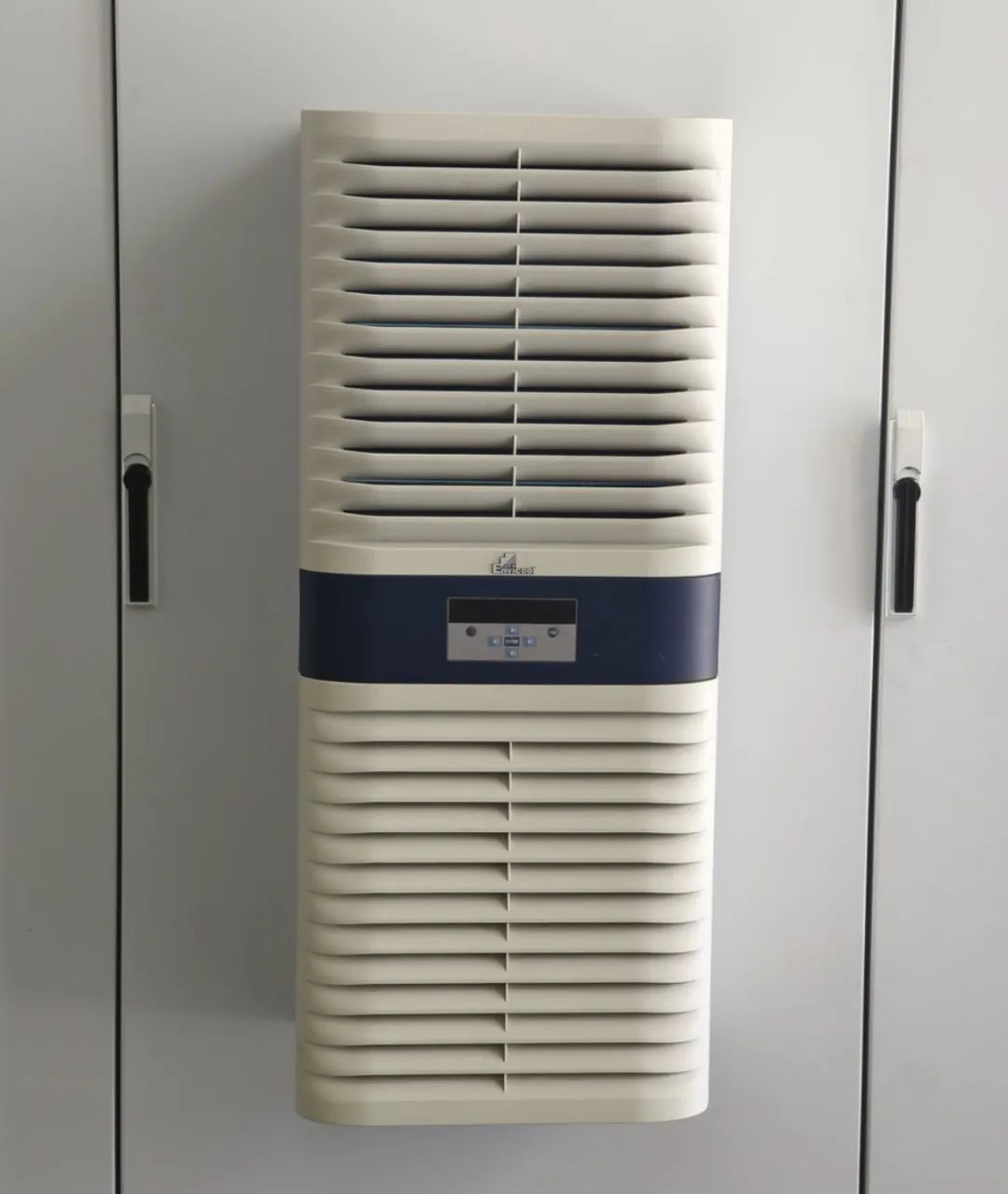
Clogging or damage to the cooling system can cause equipment to overheat, which can lead to unexpected failures or downtime, which can have a serious impact on production. Through regular cleaning and maintenance, potential problems can be discovered and resolved in a timely manner to avoid production interruption caused by equipment faults.
Parts replacement plan
Identification and replacement cycle of wearing parts
In the maintenance of extruder equipment at high temperatures, the first need to accurately identify the wearing parts, which usually includes equipment manuals, empirical judgments or professional tools to confirm which parts are more frequently subjected to wear or damage.
Each wearing part has its own specific replacement cycle, which is determined based on the material, operating conditions and historical maintenance records of the part, to ensure that the equipment can operate in optimal condition and avoid production disruptions due to the aging of the part.
In order to reduce the impact of sudden failures, it is key to adopt a preventive replacement strategy, which involves regularly checking the status of wearing parts and replacing them before they reach their intended service life, thus guaranteeing the stable operation and productivity of the equipment.
Make replacement plan according to the actual situation
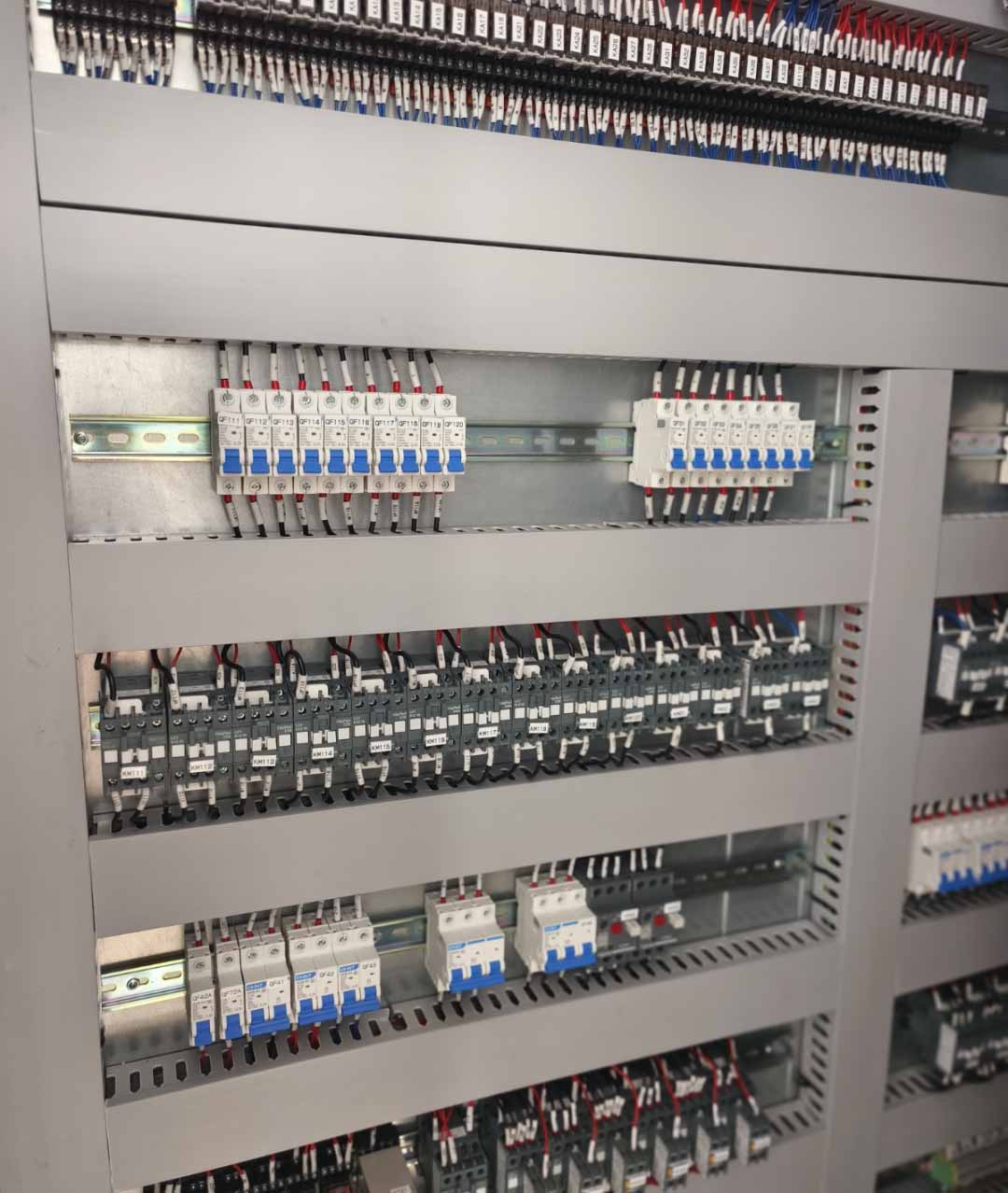
In the actual production environment, the health of the equipment may be different from the manufacturer's assumptions. Therefore, you need to adjust the replacement interval recommended by the manufacturer based on the actual running time, load, and environmental factors.
With limited resources, it is critical to determine which parts need to be replaced first. By analyzing the failure rate and maintenance cost of the equipment, the reasonable parts replacement priority can be effectively worked out to ensure the stable operation of the equipment.
Lubrication and maintenance
Easy reduction box, rolling bearing cleaning and oil change steps
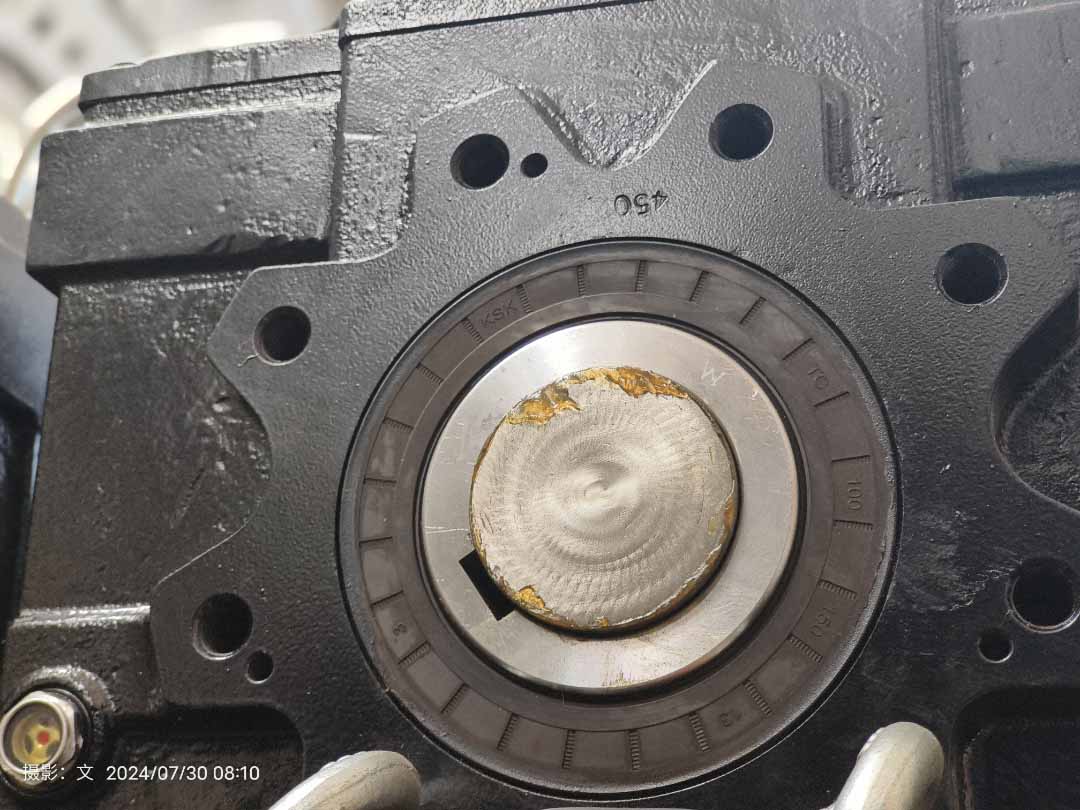
Before starting the cleaning and oil change work of the reducer, first of all, it is necessary to disconnect the power supply to ensure that the equipment stops running completely. Then release the oil in the reducer box, and prepare the cleaning agent and new lubricating oil for the next step of cleaning.
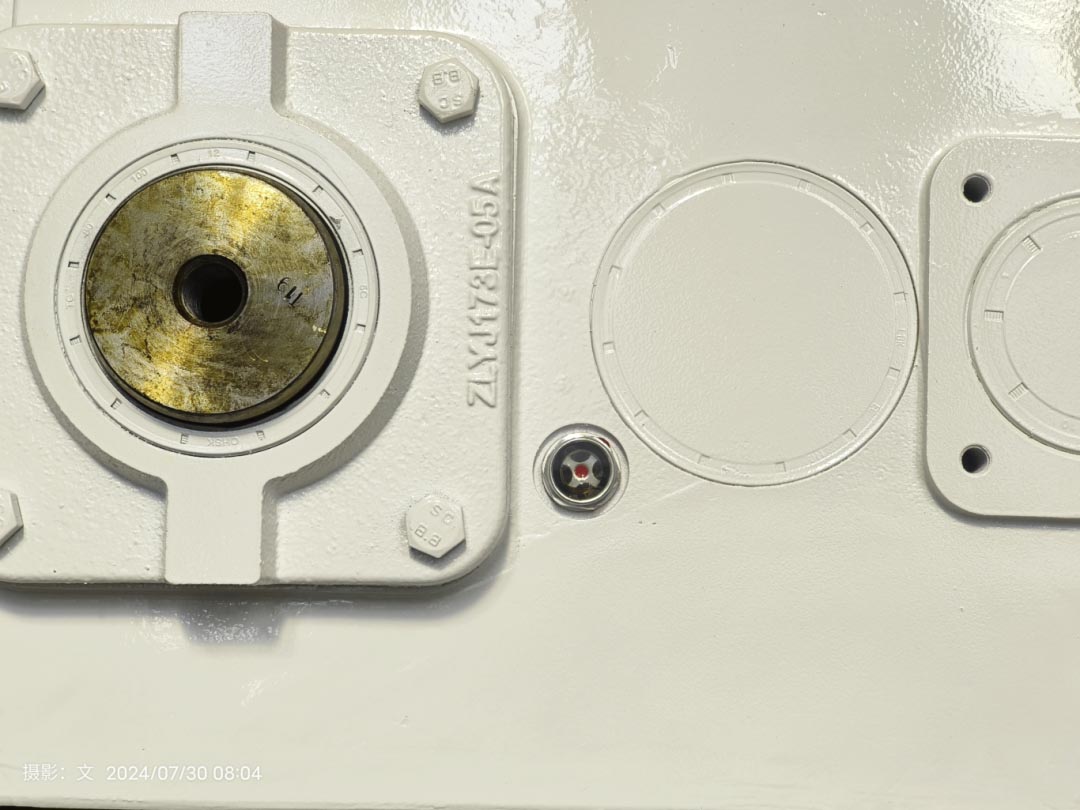
The cleaning of rolling bearings should be carried out carefully, using a soft brush and a special cleaning agent to remove old oil and impurities from the bearings and the surrounding area. After cleaning, it is necessary to dry with a clean rag and check whether the bearing is damaged or worn to ensure its good operation.
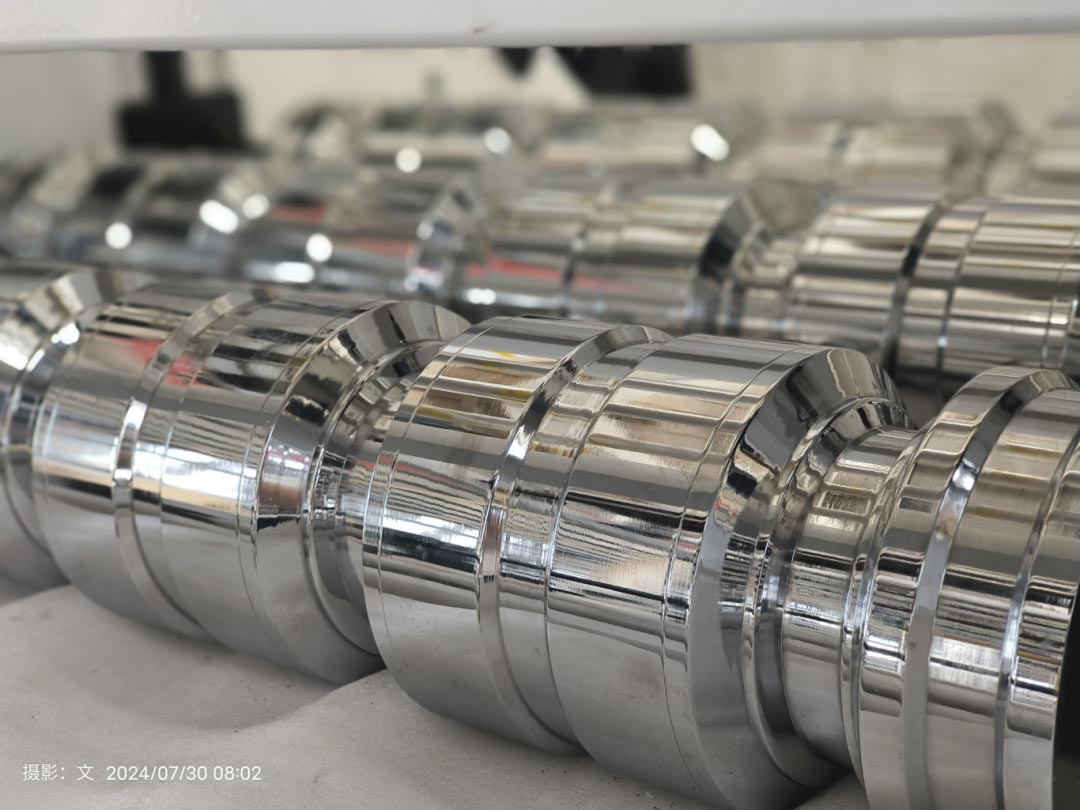
After cleaning, add new lubricating oil to the gearbox and rolling bearing to the recommended oil level. Then reassemble and start the equipment, observe whether the lubrication system is normal, no leakage phenomenon. Finally, the operation test is carried out to ensure that everything is normal before being put into production.
Regular inspection of safety devices
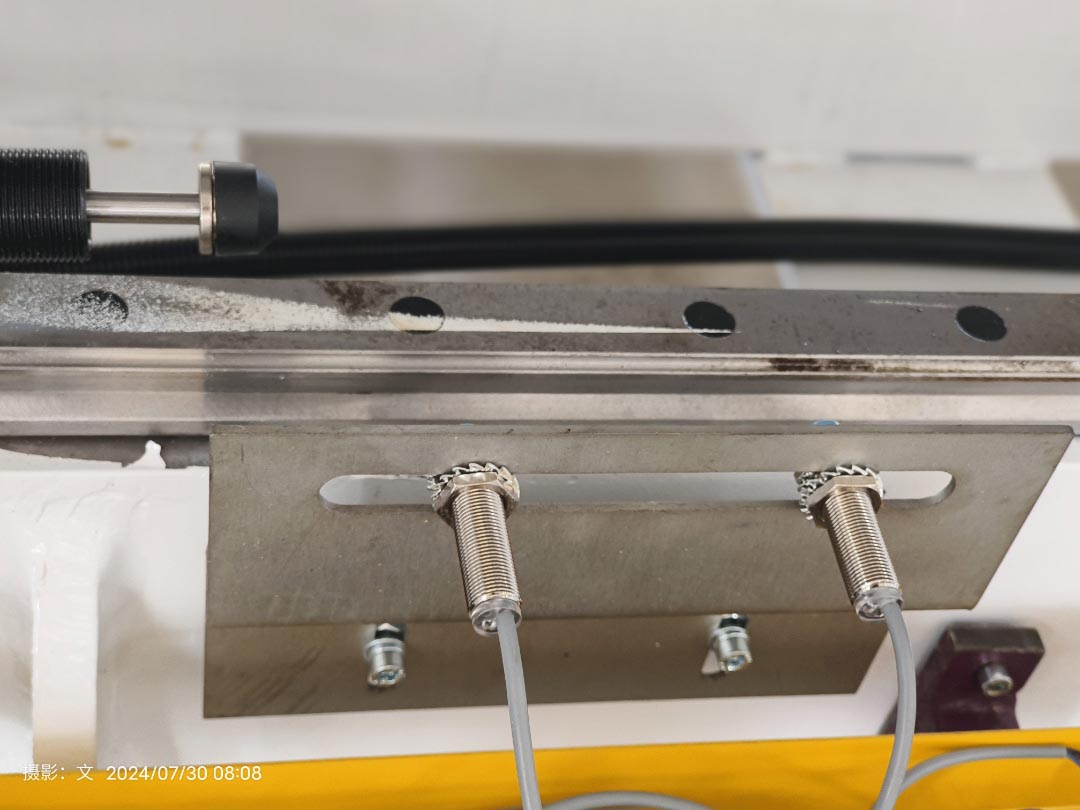
Regularly check the safety valve of the extruder to ensure that it can work normally under high temperature conditions, prevent equipment damage or safety accidents caused by valve failure, and ensure the stability of production and the safety of personnel.
The emergency shutdown system is an important safety device of the extruder, which needs regular functional testing and response time detection to ensure that the power supply can be cut off immediately when the equipment is abnormal, avoid the expansion of the fault, and protect the safety of the equipment and the operator.
The extruder operating at high temperature must be equipped with a temperature monitoring system, and set a reasonable temperature threshold, once the temperature exceeds the threshold, the alarm will be activated, and timely measures will be taken to prevent the equipment from overheating to ensure the safety and continuity of the production process.
Electrical system inspection
Safety check points of electric heating system
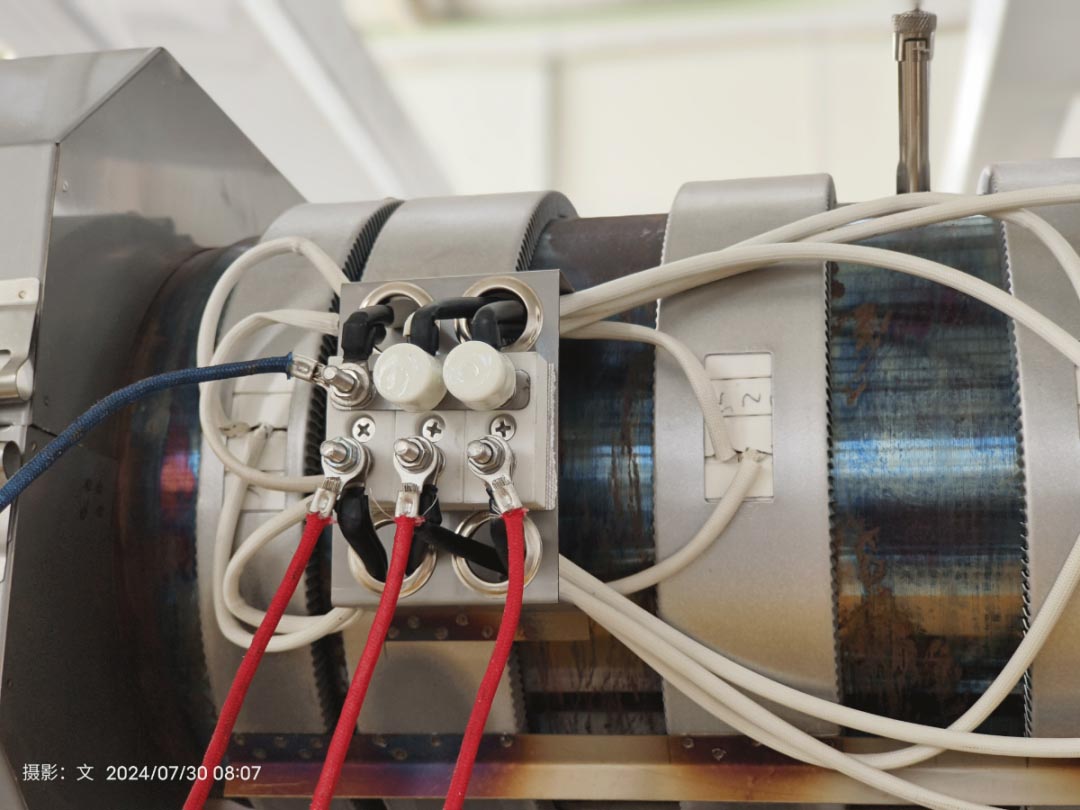
In order to ensure the safe operation of electric heating systems, insulation checks must be carried out regularly. This includes testing the insulation resistance of the heating elements, wiring and control systems to ensure there is no risk of leakage and to prevent safety incidents caused by electrical failures.
The temperature control system of extruder equipment at high temperature must be accurate and reliable to avoid damage to equipment or affect product quality due to high temperature. At the same time, the overload protection device should be equipped, which can quickly cut off the power supply when the current is abnormal and protect the electric heating system from damage.
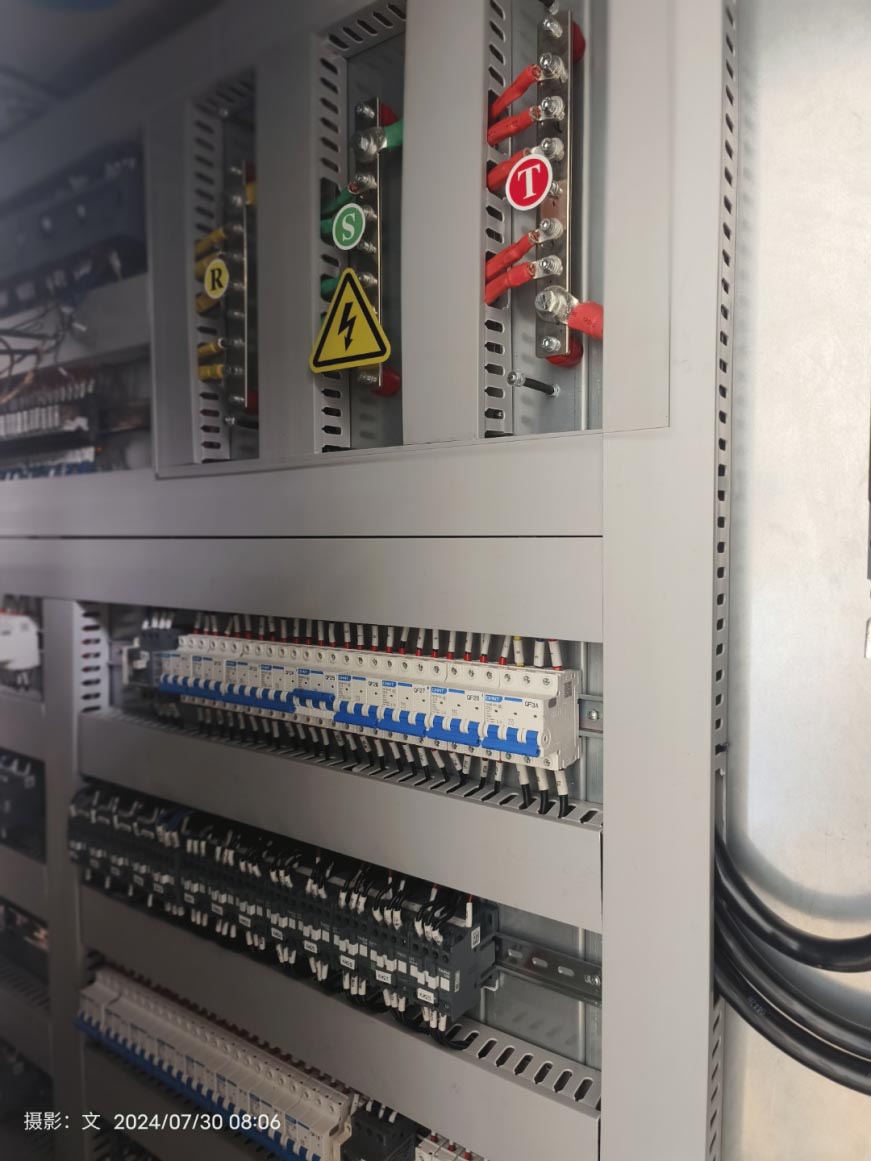
Check the aging of the heating elements of the electric heating system regularly, and replace the components that have appeared loss or performance decline in time. Ensure heating efficiency and safety to avoid equipment damage or production accidents caused by uneven heating or failure.
Accuracy verification of electrical wiring and instrumentation
In high temperature environments, the electrical wiring of extruder equipment is prone to damage, and regular inspection of the integrity of the line is a key step to ensure the safe operation of the equipment. This includes checking wires, cables, and connection points for signs of wear or loosening.
High temperature operating conditions will affect the accuracy of the instrument, and regular calibration and verification of the instrument of the extruder equipment is an important link to ensure the control accuracy of the production process and product quality.
Through the accuracy verification of electrical lines and instruments, potential faults and problems can be found in time, and corresponding preventive measures can be taken to avoid small problems evolving into major failures and ensure the stable operation of extruder equipment.
Fault prevention and handling
Common fault types and preventive measures
In a high temperature environment, extruder equipment is prone to overheating, resulting in decreased machine performance and even damage. Preventive measures include regular inspection of the cooling system to ensure that the cooling effect is good and to avoid long periods of high load operation.
The high temperature environment accelerates the decomposition and evaporation of lubricating oil, resulting in poor lubrication of the extruder and aggravating wear. Preventive measures for the use of high temperature resistant lubricants, and regularly check the amount of oil and oil quality, to maintain proper lubrication.
High temperatures pose a threat to the electronic components of the extruder, which can lead to premature aging or failure of the components. Preventive measures include the selection of high-temperature resistant electronic components, increasing the heat dissipation design of the equipment, and regular functional testing and maintenance of the electronic equipment.
Emergency handling procedure when a fault occurs
Once the extruder equipment is found to be abnormal, the first measure is to immediately stop the operation of the equipment to prevent the expansion of the fault. This is followed by a comprehensive inspection of the equipment to determine the specific location and cause of the failure.
In case of emergency, contact the professional maintenance team to provide technical support. Ensure that the maintenance team can arrive at the site in time to diagnose and handle faults professionally, so as to shorten the repair time.
While waiting for the arrival of the professional team, take temporary measures according to the fault situation, such as shutting down the relevant system, isolating the fault part, etc., to avoid the fault affecting other equipment or production process, and reduce losses.