Chemical name: Acrylonitrile Butadiene Styrene Copolymer
English name: Acrylonitrile Butadiene Styrene
Specific gravity: 1.05 g/cm³
Molding shrinkage: 0.4-0.7%
Molding temperature: 200-240℃
Drying conditions: 80-90℃ for 2 hours
Characteristics of ABS plastic
Good comprehensive performance, high impact strength, chemical stability, and good electrical performance
Good welding performance with 372 organic glass, can be made into two-color plastic parts, and can be surface-plated with chromium and painted.
Has high impact resistance, high heat resistance, flame retardance, reinforcement, transparency, etc.
The flowability is slightly worse than HIPS, but better than PMMA, PC, etc. and has good flexibility.
Uses: ABS profiles produced by abs extruder machine are suitable for making general mechanical parts, wear-resistant parts, transmission parts, and telecommunication parts.
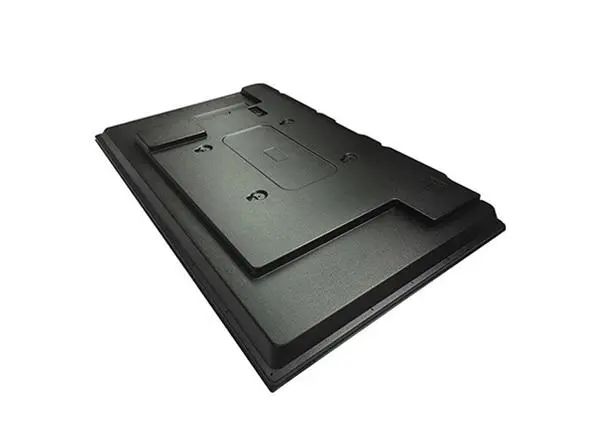
Amorphous material with medium flowability, high moisture absorption, must be fully dried, and the plastic parts with glossy surface requirements must be preheated and dried for 80-90 degrees, 3 hours.
It is advisable to use a higher material temperature and mold temperature, but the material temperature is too high and prone to decomposition (decomposition temperature is>270 degrees). For plastic parts with higher accuracy, the mold temperature should be 50-60 degrees; for high-gloss, heat-resistant plastic parts, the mold temperature should be 60-80 degrees.
If water marks need to be eliminated, the material flowability needs to be increased, and high material temperature, high mold temperature, or changing the water inlet level and other methods can be adopted.
If the molded material is heat-resistant or flame-retardant, plastic decomposition products will remain on the surface of the mold after 3-7 days of production, causing the mold surface to be shiny. It is necessary to clean the mold in time and increase the exhaust position on the mold surface.
Characteristics and basic knowledge of ABS thick sheet vacuum forming materials
ABS resin is currently the polymer with the largest production and the most widely used. It organically unifies various properties of PS, SAN, and BS, and has a balanced mechanical property of toughness, hardness, and rigidity. ABS is a terpolymer of acrylonitrile, butadiene and styrene, A represents acrylonitrile, B represents butadiene, and S represents styrene.
ABS engineering plastics are generally opaque, with a light ivory appearance, non-toxic, odorless, and have the characteristics of toughness, hardness, and rigidity. They burn slowly, with yellow flames and black smoke. After burning, the plastic softens and scorches, emitting a special cinnamon smell, but there is no melting and dripping phenomenon.
ABS engineering plastics have excellent comprehensive properties, extremely high impact strength, good dimensional stability, electrical properties, wear resistance, chemical resistance, dyeability, and good molding and mechanical processing. ABS resin is resistant to water, inorganic salts, alkalis, and acids. It is insoluble in most alcohols and hydrocarbon solvents, but is easily soluble in aldehydes, ketones, esters, and certain chlorinated hydrocarbons.
The disadvantages of ABS engineering plastics are low heat deformation temperature, flammability, and poor weather resistance.