The four-day CHINAPLAS 2024 has come to a successful end. In the busy and orderly process of each day, JWELL and our client partners have had in-depth exchanges, and we have witnessed countless wonderful moments together, leaving beautiful marks on each other.

JWELL has made its debut with multiple core solutions, focusing on the trend of high-end, intelligent, and green development in the rubber and plastic industry. Efficient and leading technological advantages, diverse application scenarios, and precise responses to customer needs and market changes have attracted industry experts and technology innovators from around the world on site, showcasing the latest trends and cutting-edge technologies in the industry by squeezing out niche fields.
Exhibition highlights
1. Pulp molding and trimming integrated machine

By utilizing renewable plant resources such as wheat straw, reeds, sugarcane bagasse, and other plant fibers, various fiber daily necessities, fiber paper tableware, fiber paper tray, fiber paper industrial product shock pads and packaging trays, non flat fiber paper decorative wall panels, and non flat fiber paper three-dimensional products are produced through molding methods.
Features:
Sucking method: reciprocating molding
Maximum product height: 100mm
Drying method: In mold drying
Forming pressure: 40-60 tons
Heating of shaping plate: thermal oil or electric heating
Product transportation method: In mold transportation
Production: 800-1000Kg/24 hours
2. CFRTP-UD unidirectional belt testing machine

This test line is mainly used for the experiment and production of CFRTP-UD unidirectional tapes. CFRTP unidirectional tapes are single-layer fiber reinforced thermoplastic composite materials with continuous fibers that have been unfolded and flattened, and then impregnated with thermoplastic resin for reshaping. The characteristics of these materials are that the fibers are arranged parallel to each other (in the 0 ° direction) without interweaving.
Technical parameters:
Basic resins: PP, PE, PET, PA6, PPS, PEEK, etc
Fiber types: glass fiber, carbon fiber, aramid, basalt fiber
Product thickness: 0.15~0.45mm
Product width: 50-300mm
Product surface density: 100-650gsm
Fiber content of the product: 40%~70%
Traction speed: 5-20m/min
3. PE stone paper production line
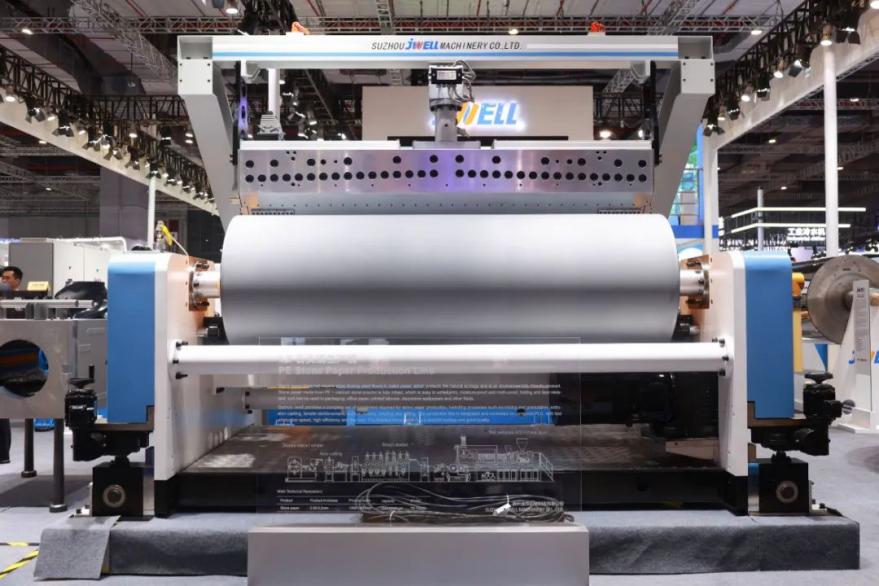
Stone paper does not require trees and uses plant fibers to make paper, protecting the natural ecology and making it an environmentally friendly product. The stone paper made of PE+calcium stone powder is fully mixed, easy to write and print, moisture-proof and moth proof, resistant to folding and tearing, and can be used in packaging, office paper, printing albums, decorative wallpapers and other fields.
JWELL Company provides a complete set of equipment required for the production of stone paper, including mixed granulation, extrusion casting, tensile reinforcement, surface coating, winding and slitting processes. The production line adopts PLC integrated control, which has fast production speed, high efficiency, and low cost. The surface of the finished stone paper is smooth and of good quality.
4. Storage and winding system production line

This winding machine is suitable for the winding of TPU film and coated products. The system adopts a control method combining servo control and tension detection to achieve a constant tension winding state.
The constant tension mode ensures that the film does not wrinkle during the winding process, and the function is smooth and beautiful. The dual station winding machine realizes the functions of automatic cutting and automatic winding, which can improve the speed of the production line, save time, and reduce manual operations.
Features:
Double station automatic winding machine
Structural form: automatic cutting. automatic flipping
Reel: Three inch spline air expansion shaft
Installation method of the winding shaft: using cylinder clamping
Winding drive: driven by servo motor
Tension sensor: Italian brand
Winding diameter: Φ 800mm
Winding width: 2000mm
Winding speed: 50m/min
5. High barrier MDOPE blow molding coating production line

5-layer co extrusion online MDO+online coating single material high barrier blown film solution
Features:
Preferred alternative to aluminum foil liquid milk bags
Easy to recycle and degrade
Microwave heating capability
OTR<0.1
Oxygen permeability<0.1
6. JWZ-BM30Plus three-layer hollow molding machine with liquid level
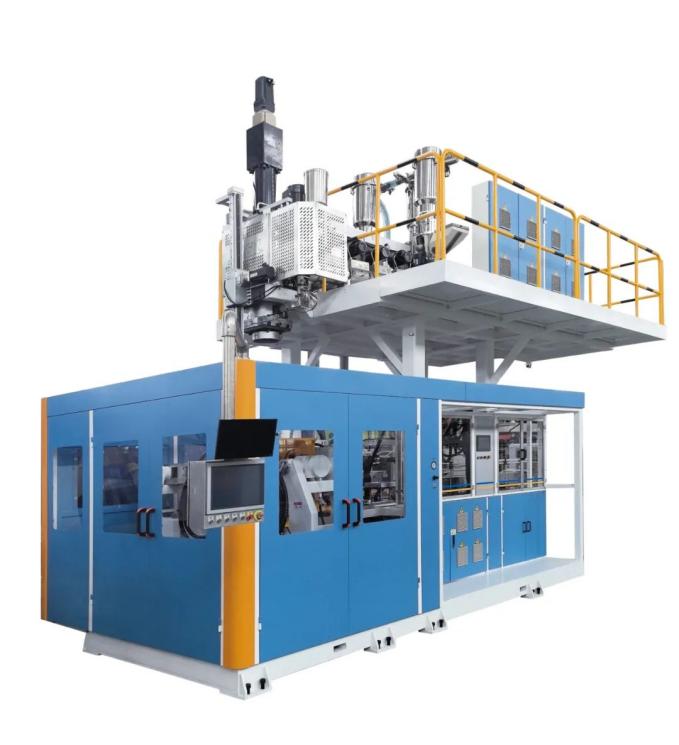
This model is suitable for the production of 20/30 liter fully automatic stacking barrel production line.
Application features:
Adopting a three-layer continuous machine head with liquid level lines, two U-shaped mold frames, and a bottom blowing structure. Equipped with automatic feeding machine, online automatic trimming, one strong cold shaping, three auxiliary shaping, online product leakage detection, reserved online weighing and coding stations, and online conveying and crushing of trimming. The intelligent hollow blow molding machine production line with unmanned and less human operation will greatly reduce labor intensity and improve production efficiency.
Adopting the Baccarat automation control system, supporting multi task and time-sharing operations, with a high degree of automation; The advanced human-machine interface replaces the conventional panel function control system, and the new generation of programmable computer controllers represents a new level of industrial control, integrating the functions of PLC and industrial computers. Operating programs (parameters) can be stored. Centralized display of the overall operating status, open architecture, and fieldbus interface.
The mold base adopts the JW 5th generation two plate U-shaped structure, and the mold closing is driven by servo swing arm rotation, with low friction resistance, good motion characteristics, and high mold closing accuracy. In order to maintain stability and cost-effectiveness, the sub mold locking is equipped with a power pack. Compared with conventional hydraulic models, electric blow molding can significantly increase production, reduce energy consumption, and reduce product pollution. The mold frame has the characteristics of uniform mold locking, large mold locking force, large capacitive modulus, and more convenient mold disassembly and assembly.
Adopting a continuous three-layer liquid level line mold head, while ensuring the stretching and compactness of the material, the control of color change, layering, and product surface treatment are relatively good. Squeeze the recycled materials into the middle layer of the product, and wrap the inner and outer layers with brand new materials. The appearance of the product is the same as the brand new material, and the strength and performance of the product are improved.
The unit will shift the semi-finished products containing burrs online and place them at the deburring station. After pushing the burrs, they will be flipped to the cooling and shaping station, and cooled by high and low pressure circulating air blowing. Continuously use low-temperature dry air circulation cooling to shorten the molding cooling time. Subsequent auxiliary shaping+online leak detection and weighing.
The entire machine is powered by servo motors, with a total of 5 sets of servo motors.
Although the exhibition has come to a successful conclusion, the excitement will not stop.
Sincere thanks to every visitor and friend who visited the exhibition site, and grateful for the trust and support of every customer partner. Grateful meeting, looking forward to reuniting with you again!