Polyetherketoneketone (PEKK), also known as PAEK, is a crystalline polymer formed by connecting aromatic rings through oxygen bridges (ether bonds) and carbonyl groups (ketones). Depending on the sequence and proportion of ether bonds, ketone groups, and benzene rings in the molecular chain, various polymers can be formed.
The molecular structure of PEKK contains rigid benzene rings, providing stiffness, while the presence of ether bonds imparts flexibility. This allows it to be processed using thermoplastic engineering plastics manufacturing methods.
Jwell plastic machinery takes you into the world of PAEK. The types of PAEK discussed today include polyetheretherketone (PEEK), polyetherketone (PEK), polyetherketoneketone (PEKK), polyetheretherketoneketone (PEEKK), and polyetherketoneetherketoneketone (PEKEKK).
Performance of Different PAEK Categories
The differences between various types of PAEK lie in their chemical composition, the sequence, and proportion of ether ketones. Since the ratio of ether to ketone units affects the glass transition temperature (Tg) and melting temperature (Tm), each type of PAEK exhibits different characteristics, with high ketone content varieties having both high Tg and Tm.
PEEK
Polyetheretherketone
Polyetheretherketone (PEEK), the first industrially produced variety, has the following chemical structure:
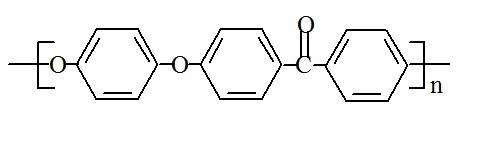
PEEK's chemical name is poly(oxy-1,4-phenylenoxy-1,4-phenylene carbonyl-1,4-phenylene), and its CAS number is 31694-16-3.
PEEK is a high-performance engineering plastic with excellent heat resistance, water resistance, solvent resistance, and electrical insulation properties. It has high fatigue strength, superior radiation resistance among all plastics, a high oxygen index, and produces minimal smoke and toxicity during combustion.
PEK
Polyetherketone
Polyetherketone (PEK) has the following structure:
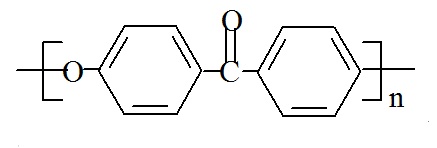
PEK's chemical name is poly(oxy-1,4-phenylene carbonyl-1,4-phenylene), and its CAS number is 273870-27-4.
PEK has a higher melting point and glass transition temperature than PEEK due to the lower proportion of ether bonds and ketone groups in its molecular structure. It exhibits better heat resistance than PEEK, with a continuous use temperature of 250°C.
PEKK
Polyetherketoneketone
Polyetherketoneketone (PEKK) has the following structure:
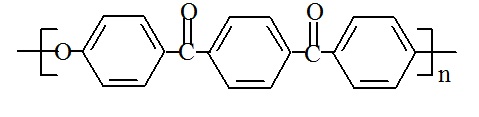
PEKK's chemical name is poly(oxy-1,4-phenylenecarbonyl-1,4-phenylenecarbonyl-1,4-phenylene), and its CAS number is 74970-25-5.
PEKK's performance varies depending on the specific acyl chloride used as the monomer. PEKK synthesized using terephthaloyl chloride as the raw material has the highest glass transition temperature and melting point among the main types of PAEK. PEKK synthesized using isophthaloyl chloride exhibits slightly lower melting and glass transition temperatures. In practice, PEKK is often produced using a mixture of terephthaloyl chloride and isophthaloyl chloride as raw materials.
PEEKK
Polyetheretherketoneketone (PEEKK) has the following structure:
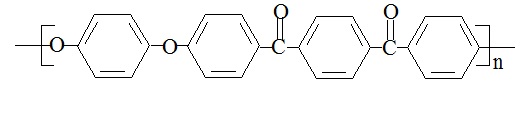
PEEKK's chemical name is poly(oxy-1,4-phenyleneoxy-1,4-phenylenecarbonyl-1,4-phenylenecarbonyl-1,4-phenylene), and its CAS number is 60015-03-4.
PEEKK has a similar proportion of ketone groups and ether bonds as PEK, resulting in similar melting points and glass transition temperatures to PEK. It also exhibits excellent heat resistance, mechanical strength, and rigidity.
PEKEKK
Polyetherketoneetherketoneketone (PEKEKK) has the following structure:
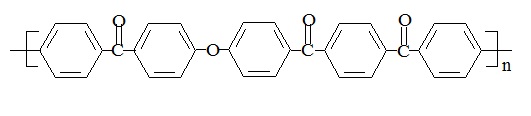
PEKEKK's chemical name is poly(oxy-1,4-phenylcarbonyl-1,4-phenyleneoxy-1,4-phenylenecarbonyl-1,4-phenylenecarbonyl-1,4-phenylene), and its CAS number is 60015-05-6.
PEKEKK is an important variety that follows PEEK. It has excellent mechanical properties, high strength, and large rigidity. It exhibits reliable fatigue resistance and can be continuously used at temperatures ranging from 250-260°C. Even the unfilled grade of PEKEKK has a limited oxygen index of only 36%, meaning it achieves UL94 V-0 rating without the addition of any flame retardants. It has good electrical insulation performance, excellent wear resistance, and stability against nearly all chemical substances. It exhibits good water resistance, hot water resistance, and steam resistance. Additionally, it has excellent radiation resistance.
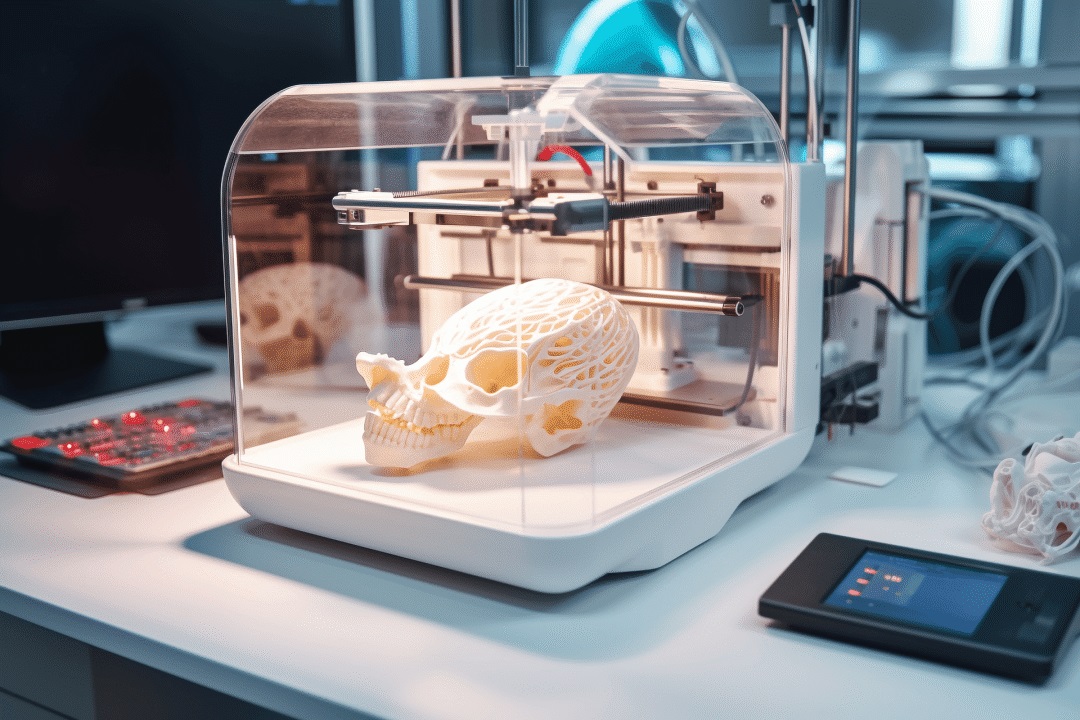
Modification of PAEK Materials
Hyperbranched PAEK
Hyperbranched polymers, with their highly branched structure and low chain entanglement characteristics, exhibit unique properties such as high solubility, low viscosity, high rheology, and a large number of end functional groups. In recent years, numerous hyperbranched PAEK materials have been synthesized to expand the application areas of PAEK. For example, Shu Chingfong et al. prepared a series of hyperbranched PAEKs using AB-type monomers through electrophilic substitution reactions, and the structure and branching degree of the hyperbranched PAEKs were determined.
Cyclic PAEK
Synthesizing cyclic PAEK and then using ring-opening polymerization to produce linear PAEK with high relative molecular weight has several advantages over conventional condensation reactions. Firstly, cyclic low oligomers with low relative molecular weight generally have good solubility, low melting points, and low melt viscosities. Secondly, the polymerization conditions are mild, allowing the production of polymers with special structures that cannot be obtained through condensation reactions. Thirdly, ring-opening polymerization does not produce small molecular by-products, ensuring the stability and balance of material properties. Finally, ring-opening polymerization involves the self-polymerization of cyclic oligomers, maintaining a constant amount of material, and facilitating the production of high molecular weight polymers.
Yang Liguo et al. have successfully synthesized electroactive cyclic PAEKs by overcoming spatial effects. Due to their unique porous structure, excellent electrical activity, and outstanding environmental stability, these materials have attracted widespread attention.
Thermotropic Liquid Crystalline PAEK
Liquid crystals exhibit unique temperature effects, photoelectric effects, magnetic effects, and good mechanical properties, making them widely applicable in electronics, television displays, temperature sensing, and engineering. G.S. Benet et al. used commonly used liquid crystal monomers, such as biphenol monomers and crystallization-disrupting monomers substituted with benzophenone, as two types of bisphenol monomers, and 4,4'-difluoro(2-benzophenone) as a dihalide monomer. They successfully synthesized a series of thermotropic liquid crystalline PAEKs through high-temperature solution copolycondensation, reducing the melt viscosity of PAEK.
Sulfonated PAEK
One of the most studied functionalizations of PAEK is sulfonation, which is used to produce functional membranes or for fuel cells. Ni Hongzhe et al. used nucleophilic substitution reactions to synthesize a series of PAEK sulfonated membranes with different degrees of sulfonation by copolymerizing sulfonation monomers and non-sulfonated monomers of tert-butyl hydroquinone. It was found that the proton conductivity of the PAEK sulfonated membrane with a sulfonation degree of 0.8 reached 0.061 S/cm at 80°C, which is close to Nafion117 membrane. Furthermore, its methanol permeability coefficient was 3.4×10-7 cm2/s, much lower than that of Nafion117, indicating promising applications in proton exchange membrane fuel cells and direct methanol fuel cells.
Introducing Semiflexible Groups into the PAEK Polymer Chain
Introducing semiflexible groups such as sulfone, sulfide bonds, and substituted methylene into the PAEK polymer chain can improve the toughness of PAEK. Tong Yongfen et al. used four monomers, namely 2,2'-dimethyl-4,4'-diphenoxy diphenyl sulfone, diphenyl ether, p-benzoyl chloride, and m-benzoyl chloride, in certain proportions. Under the presence of anhydrous AlCl3 and N,N-dimethylformamide, a low-temperature solution copolycondensation reaction was carried out in 1,2-dichloroethane to synthesize PAEK/polyarylether sulfone ketone random copolymers with methyl side groups. These copolymers exhibited high Tg (glass transition temperature) but lower melting temperature, and their thermal decomposition temperatures were above 450°C, showing good solvent resistance.
Introducing Rigid Groups into the PAEK Polymer Chain
Introducing rigid and heat-resistant structural units such as biphenyl, naphthalene, anthracene, and aromatic heterocycles into the PAEK polymer chain can enhance the heat resistance of PAEK. Generally, the higher the aromatic content in PAEK, the better the heat resistance of the resin. M. Ohno et al. synthesized PEK with both naphthalene rings and alkyl groups in the main chain via nucleophilic reactions. These PEK polymers exhibited high Tg and good solubility.
Introducing Side Groups into the PAEK Polymer Chain
Introducing side groups such as phenolphthalein, alkyl groups, and halogen atoms into the PAEK polymer chain can reduce the regularity of the molecular chain, lower the melting temperature and crystallinity of PAEK, significantly improve the solubility, and allow for processing techniques such as coating and extrusion, or functionalization of PAEK. Liu Baijun et al. synthesized fluorinated PAEK with low dielectric constant, low refractive index, and low water absorption. It also improved thermal stability, solubility, and flame retardancy while increasing transparency.
PAEK Copolymerization and Blending Modification
Copolymerization plays a significant role in modifying PAEK, and there have been many studies in this area. Cai Mingzhong et al. synthesized a series of PEKEKK/random copolymers containing naphthalene rings through low-temperature solution copolycondensation reactions. The copolymers exhibited higher Tg than pure PEKEKK, while the melting temperature and crystallinity gradually decreased with increasing content of naphthalene ring units in the copolymers. The copolymers showed excellent heat resistance and corrosion resistance. Blending modification is also an effective approach to obtain blends with excellent properties by combining two different polymers. In recent years, successful blending modifications have been achieved by blending PEK resins with polyether sulfone, polyarylates, polyphenylene sulfide, and other high-performance resins.
Applications of PAEK
Aerospace Industry
As one of the first thermoplastic materials to be used in the aerospace industry, PAEK has become an indispensable part of aerospace materials. The most widely used is PEEK, which is employed for manufacturing internal components of aircraft due to its excellent flame retardancy, low smoke and toxic gas emissions during combustion. Additionally, PEEK is used to make battery casings, bolts, nuts, and internal parts of rocket engines.
Industrial Sector
In the automotive manufacturing industry, PAEK can replace stainless steel and titanium for manufacturing engine covers. Various components such as bearings, gaskets, seals, and clutch gears made from PAEK are widely used in the transmission, braking, and air conditioning systems of automobiles. PAEK is also utilized in the production of wire cables, coil frames, electronic insulation films, and various connectors, which have been successfully applied in nuclear power plants.
Medical Field
PAEK's high temperature resistance makes it suitable for manufacturing sterilization equipment components. It is also used in surgical and dental devices that require high performance and repeated use. Furthermore, PAEK's non-toxicity, lightweight, and corrosion resistance make it valuable for organic integration with the human body, serving as a substitute for metallic materials in the manufacturing of human bones. Its application in the medical field has significant implications.
PAEK has wide-ranging applications in other fields as well. With the development of technologies such as 3D printing and carbon fiber reinforcement, new techniques and fields are expected to demand higher requirements for PAEK.